Blast Room Introduction
Blast room equipments used in a wide variety of industries that require surface preparation prior to application of a protective coating. The surface of the work piece is cleaned by a mixture of abrasive and high pressure compressed air being directed at the work piece by blast nozzle.
Finiprak offers a variety of blast room designs and room configurations which allow us to design a blast room facility uniquely tailored to meet the economic production, safety and environmental concerns of each customers. The layouts of complete Blast Room System are always different from plant to plant, every blast room must be designed independently depending upon the customer's requirement.
Finiprak offers variety of Blast Room designs and system configurations which allow us to design a blast room facility uniquely tailored to meet the economic production, safety & environmental concerns of each customers.
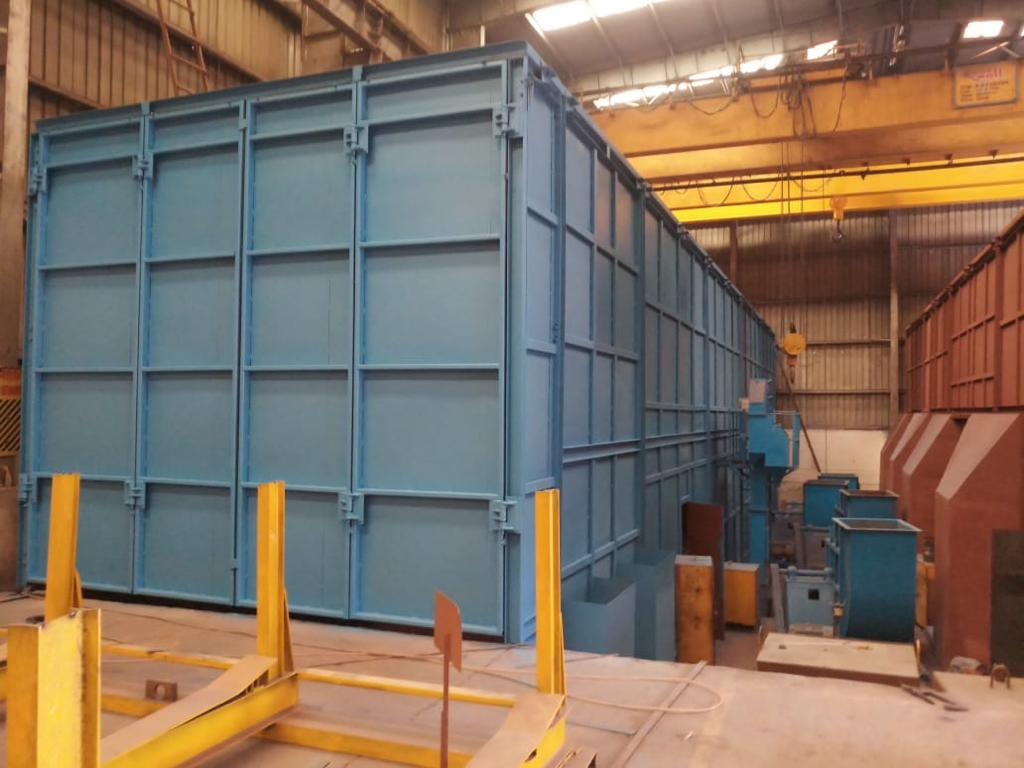
Blast Room The Enclosure
The modular blast room is specially ventilated and illuminated for enclosed abrasive blasting, and is a fully sealed, dust tight, all steel structure. The components are prefabricated for simple bolt-together erection, with little or no job site welding required. The enclosure stands by it's own structural support without connections to the surrounding facilities. Internally, the enclosure has no areas, other than the floor, where airborne media or dust may be captured. The size of the enclosure depends on.
- The size of the job
- Number of operators
- adequate working space around the job.
Blast Room Essential Parts
An efficient Blast Room System consists of:
- enclosure
- Abrasive Blasting Machine
- Safety Wears
- Dust Collectors
- Blasting Media Recovery & Separation System
- Optional Equipment
Blast Room Blasting Machine & Safety Equipment
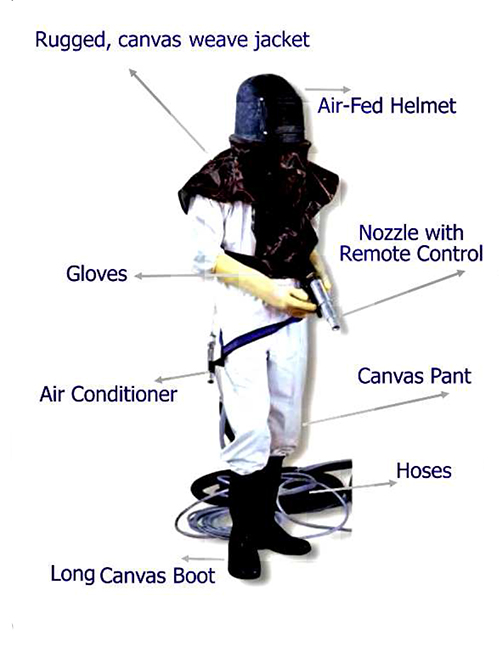
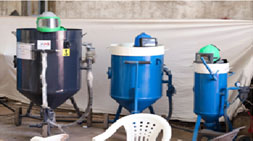
Blast Rooms are generally provided with P7-501R and P7-1001R models. During the blasting process, the dump valve and exhaust valves are closed, the vessels is pressurized and the media is forced out through the feed valve to the nozzle. When the blasting ceases, the vessel is de-pressurized by opening the exhaust valve. The vessel remains de-pressurized except when blasting is in process.
The remote control valve provide in the system releases the pressure, stopping the blasting process thereby ensuring safe working conditions for the operator in case the hose & nozzle drops accidentally.
Application Before & After Blasting
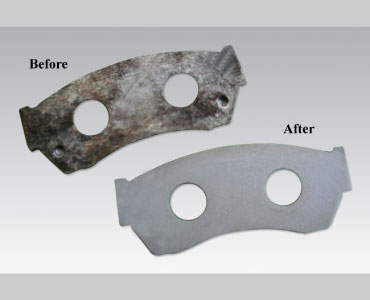
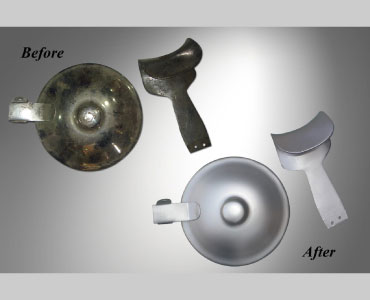
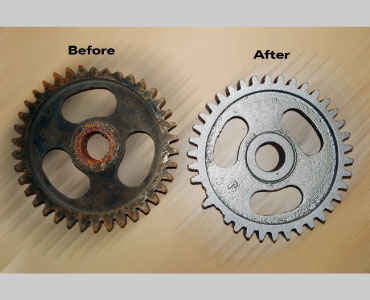
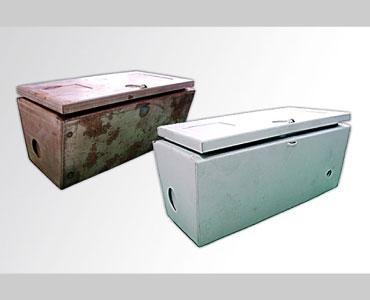